How an exhibition company achive 30% more revenue by adjusting their design workflow
- Exhibit Sync
- Apr 11, 2024
- 2 min read
Updated: May 2, 2024
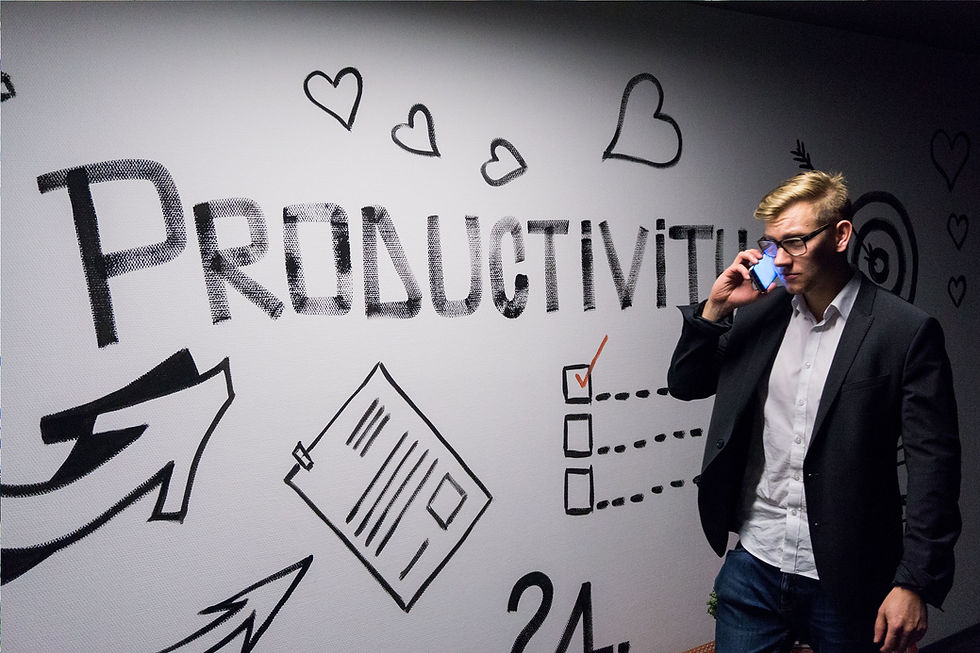
CASE STUDY
Company background:
ABC Exhibition Design Company has been in the industry for over a decade, specializing in creating captivating exhibition stands for clients across various sectors. Despite their expertise, they faced common challenges in their design-to-production workflow, including time-consuming processes, limited capacity for new projects, and difficulties meeting client deadlines.
At ABC Exhibition Design Company, the current workflow entails a multi-step process.
It begins with a design request accompanied by a detailed briefing of the client's needs. A designer then initiates the design process by translating these requirements into a conceptual stand design. However, this involves using multiple software applications, including 3D Max for 3D modeling, AutoCAD for plans, details, and elevations, Photoshop for enhancing renders, and PowerPoint for final presentations.
Additionally, a separate team member is tasked with creating a budget from scratch, meticulously detailing the pricing for each element proposed in the design.
Once the design is aproved, a technician takes over to generate specifications for production, ensuring that all requirements are met and that the design can be effectively translated into reality.
Challenges faced:
Time Constraints: The design process often took longer than anticipated, leading to tight deadlines and rushed production schedules.
Limited Capacity: The typical timeframe for completing a standard stand design averages around 5 days, limiting the company to approximately 4 projects per month per designer. To increase output, the company would need to consider hiring additional personnel, which can incur significant costs.
Inefficiencies: Manual processes and lack of standardized procedures resulted in errors, rework, and wasted resources, affecting profitability.
Costly licenses: Using multiple softwares increase the cost in licensing.
Solution Implementation:
In response to these challenges, ABC Exhibition Design Company implemented our solution. This involved:
All in one software: 3D modeling, rendering, planning, specifications, and budgeting all within a single platform. With one license, enjoy cost savings while streamlining your design process.
Centralized Asset Management: Establishing a centralized library for 3D assets enabled easy access and reuse of existing assets, eliminating the need for re model.
Standardized Protocols: Implementation of standardized protocols for version control, file management, and asset naming ensured consistency and accessibility across all projects.
Training and Support: Providing comprehensive training and ongoing support to their team ensured smooth transition and adoption of the new workflow.
Results and Benefits:
The implementation of the streamlined workflow solution yielded significant benefits for ABC Exhibition Design Company:
Increased Efficiency: The design-to-production process, which previously took an average of 5 days, was now completed in just 2 days, liberating more than 50% of the time.
Enhanced Capacity: With shorter project timelines and optimized processes, ABC could take on more projects simultaneously, expanding their capacity and revenue potential.
Improved Client Satisfaction: Faster turnaround times and higher-quality deliverables resulted in improved client satisfaction and strengthened relationships.
Enhanced Profitability: By minimizing errors, reducing rework, and maximizing resource utilization, ABC achieved greater profitability and ROI on each project.
In conclusion, the implementation of a streamlined workflow solution revolutionized ABC Exhibition Design Company's operations, enabling them to overcome common industry challenges, increase efficiency, and maximizing the profitability by improving their design-to-production process.
Comentarios